Optimizing every nook and cranny becomes paramount in modern homes where space is at a premium and every square foot counts.
While venting a dryer through the roof might seem like an efficient space-saving solution, several potential challenges accompany it.
Below, we’ll explore the problems associated with roof venting of dryers, interspersed with relevant resources for a better understanding of roof-related issues.
1. Moisture Complications
Before delving into the specifics, it’s worth noting that moisture issues are among the primary concerns when considering roof-based venting.
The elevation and design can lead to moisture retention, causing related problems.
Accumulation Issues: Moisture can easily build up when venting through the roof. This can lead to condensation within the vent, causing dampness over time.
Weather Woes: The external position of a roof vent exposes it to rain, snow, and other elements.
This could lead to external moisture entering the vent. If you’re facing weather-related roof issues, consider checking out the best RV roof coating to protect against weather extremes.
Mold Concerns: With dampness comes the risk of mold and mildew. Such growths are harmful to both the house structure and its inhabitants.
Vent Lifespan: Excess moisture could corrode and degrade vent materials quickly, leading to the need for replacements sooner than expected.
2. Maintenance & Cleaning Dilemmas
Maintenance is pivotal for any home infrastructure, and with roof-based venting, the challenges multiply.
The location, in particular, introduces a set of unique maintenance concerns.
Accessibility Issues: Cleaning a vent positioned on the roof is undoubtedly more challenging.
It’s harder to reach, making routine checks and maintenance difficult. For other roofing maintenance considerations, see how furring strips under metal roofing can play a role in effective roof management.
Professional Dependency: Due to the vent’s tricky location, you might have to regularly hire professionals for cleaning, increasing maintenance costs.
Weather Damage: The external vent can be harmed by hail or strong winds, possibly requiring you to explore roof coating for shipping containers or roof coating for asphalt shingles for protection.
3. Fire Risks
The heightened fire risk may be the most alarming concern about venting dryers through the roof.
Lint accumulation, blockages, and other issues make this a critical area of attention.
Lint Accumulation: A vertical vent system can trap lint, posing significant fire hazards.
Moreover, rust on roofing materials can exacerbate these risks. To tackle rust, explore the paint for rusted galvanized metal roofs.
Longer Vent Length: With the need for longer vents for roof routing, there’s an increased likelihood of lint blockages.
Overheating: A blocked vent can cause the dryer to overheat, raising the chances of fires.
4. Efficiency Concerns
Efficiency is at the core of any appliance’s operation. With roof-based dryer venting, several issues can curtail the efficiency of your dryer, leading to various challenges.
Increased Drying Times: A compromised vent system can mean your clothes take longer to dry, consuming more energy.
Elevated Energy Consumption: A less efficient dryer leads to higher bills and a bigger carbon footprint.
5. Installation Concerns
Installation intricacies matter. Setting up a vent through the roof isn’t just about routing; it encompasses a range of considerations to ensure longevity and functionality.
Complex Installations: Installing a roof vent requires meticulous sealing to prevent leaks.
Venting specifics, especially for roofs, can be intricate. For instance, see how to properly vent a metal roof or choose the right roof vent for a kitchen exhaust fan.
Potential for Errors: Roof work can impact its structural integrity if not done correctly. Improper installations can lead to issues like vented drip edge problems.
Solutions and Alternatives
Awareness of problems should ideally lead to solutions. If roof venting poses challenges, what are the feasible alternatives?
Side Venting: Consider venting through the side of the house as a viable alternative, reducing many of the challenges associated with roof venting.
Booster Fans: For homes where long vent runs are unavoidable, using a booster fan can help improve efficiency and reduce lint buildup.
Regular Maintenance: Whichever venting route you choose, regular maintenance is crucial. Checking for clogs, cleaning out lint, and ensuring smooth airflow can mitigate many problems.
Conclusion
While venting a dryer through the roof might appear as a space-saving solution, it is essential to consider its potential problems.
From maintenance challenges to reduced efficiency and increased fire risks, homeowners must weigh the pros and cons before deciding on this venting approach.
Always consult professionals before changing your home’s venting system to ensure safety and optimal performance.
Frequently Asked Questions
Is it OK to vent a dryer out of the roof?
Yes, it’s technically possible and permissible to vent a dryer out the roof, and it’s a method used in many homes, especially those without a convenient side wall for venting.
However, this method comes with its own set of challenges. Venting through the roof can lead to more frequent clogs due to lint accumulation increased potential for moisture problems, and can make maintenance and cleaning more difficult.
Additionally, certain building codes and homeowner association guidelines may stipulate roof venting, so it’s crucial to check local regulations and consult professionals before proceeding.
How far can a dryer vent be from the roof?
The maximum allowable distance for a dryer vent depends on various factors, including the type and model of the dryer, the type of duct material, and the number of bends in the ductwork.
Typically, for every 90-degree turn, it’s recommended to reduce the total vent distance by 5 feet, and for every 45-degree turn, reduce by 2.5 feet.
Some modern dryers allow for longer vent distances, but it’s essential to consult the manufacturer’s guidelines.
If you’re venting through the roof, ensure that the total distance (including reductions for bends) does not exceed the manufacturer’s recommendations.
Additionally, the vent should terminate at a point that’s easily accessible for cleaning and maintenance.
Is venting a dryer into the house safe?
Venting a dryer into the house is generally not recommended.
While some might consider it as a way to add heat during colder months, there are several risks involved:
Moisture: Dryers expel a significant amount of moisture, which can lead to mold growth, damage to walls and ceilings, and an increase in indoor humidity levels.
Air Quality: The vented air can contain lint, fabric softener particles, and other contaminants that can degrade indoor air quality and harm individuals with respiratory issues or allergies.
Fire Hazard: The lint expelled can be a fire risk if not adequately managed. Products marketed as indoor dryer venting systems often incorporate water traps to catch lint and moisture.
While these might mitigate some risks, they don’t address all the concerns about moisture and indoor air quality.
What happens if a dryer is not vented properly?
Improper venting of a dryer can lead to several problems:
Reduced Efficiency: The dryer will need to work harder and longer to dry clothes, leading to increased energy consumption and wear on the appliance.
Moisture Problems: Without proper venting, moisture expelled by the dryer can get trapped, leading to mold growth and potential damage to walls, ceilings, and other structures.
Fire Risk: Lint, which is highly flammable, can accumulate in improperly vented systems, leading to an increased fire risk.
Health Concerns: The reduced air quality from improperly vented dryers can exacerbate respiratory issues, allergies, and other health concerns.
It’s essential to ensure that dryer venting is done following manufacturer guidelines and local building codes to avoid these problems. Regular maintenance and cleaning of the vent system are also crucial.
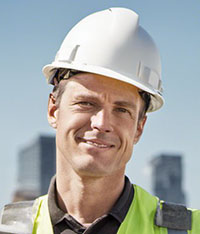
Arthur is a skilled roof worker with over 10 years of experience in the industry. He started his career as an apprentice and worked his way up to become a foreman.
When he’s not working on roofs, John enjoys with his family or writing posts. He is also a passionate cyclist.